Lean Concepts Unlock New Ways to Process Waste at the Savannah River Site
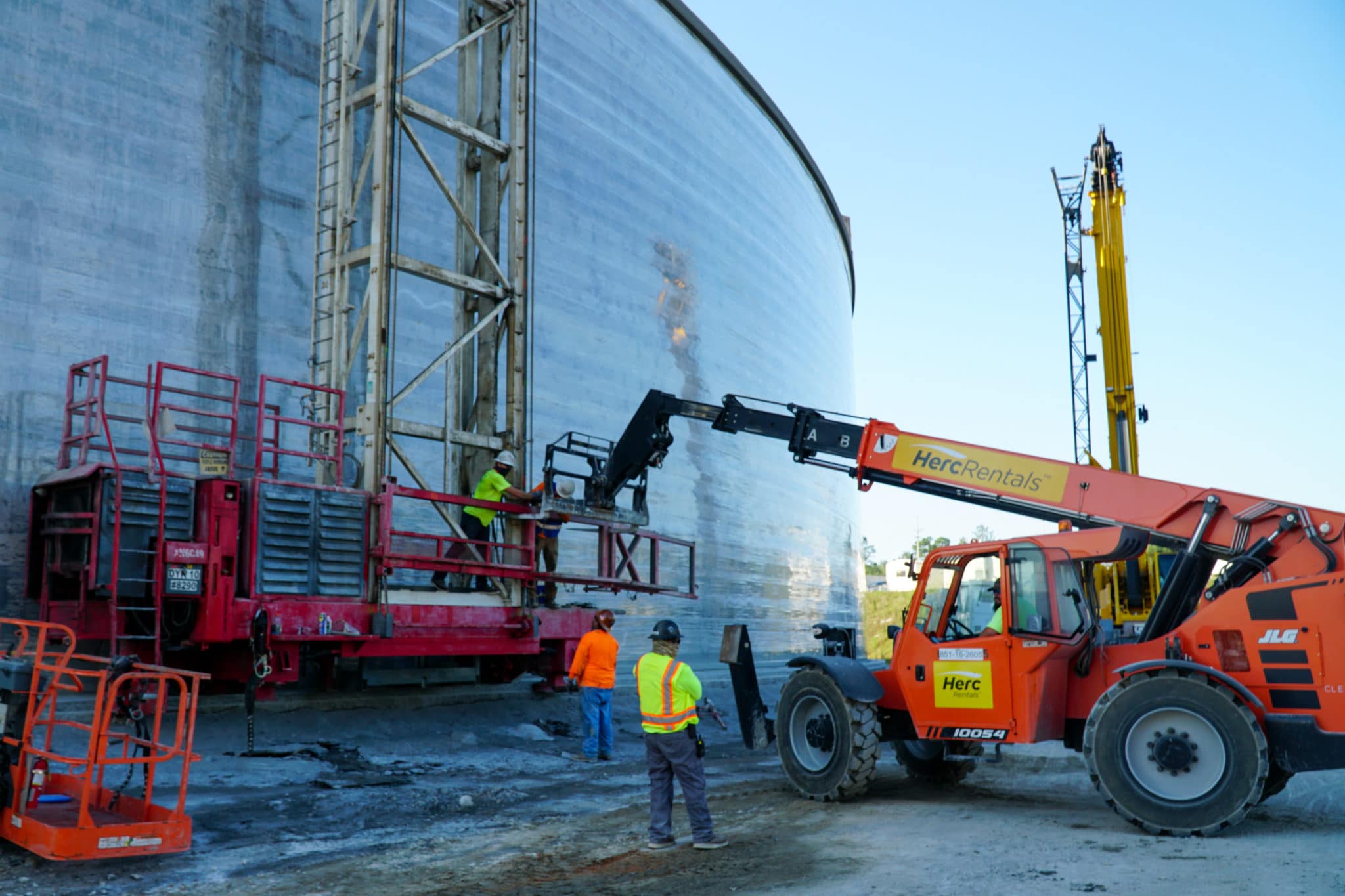
Lean Concepts Unlock New Ways to Process Waste at the Savannah River Site
By Curt Albee
Savannah River Remediation Mission Excellence Team Lead
Proven procedures and reliable routines are paramount in the nuclear business. However, even in nuclear circles, safely challenging the status quo is crucial to continuously improve. To do that, you have to focus on the forest and the trees.
That’s exactly what we do in the Mission Excellence group at Amentum-led Savannah River Remediation (SRR), the radioactive liquid waste contractor for the U.S Department of Energy (DOE) at the Savannah River Site (SRS) near Aiken, SC. A significant part of that work involves treating and safely disposing of approximately 35 million gallons of waste, of which 33 million gallons is radioactive salt waste, stored in 43 underground waste tanks.
The Parsons Corporation-managed Salt Waste Processing Facility (SWPF), which separates the salt waste into its high-level and low-level activity salt constituents, is now the driving force to considerably accelerate completion of the DOE’s liquid waste mission at SRS. Once the low-level activity salt fraction, known as decontaminated salt solution, is processed at the Saltstone Production Facility (SPF) into grout, it is safely disposed of onsite in permanent Saltstone Disposal Units (SDU). The remaining high-level activity fraction of the salt waste is processed through the Defense Waste Processing Facility and is immobilized in glass and stored in individual stainless-steel canisters awaiting shipment to a Federal Repository.
That’s an incredibly important mission, particularly when you consider that the radioactive liquid waste in the tanks has been identified by our state regulator as the single largest environmental risk in South Carolina.
SWPF is expected to process between six million and nine million-gallon salt batches per year. To handle this significantly larger amount of salt waste, multi-disciplined SRS teams through our Lean process have created new paths that will not just save time but will save millions of dollars over time. For example:
- Reducing the salt batch qualification process from 6 months to 6 weeks! This significant reduction will help meet salt waste processing requirements for SWPF operations. We accomplished this task by developing a new electronic application to help qualify large quantities of radioactive liquid salt waste for decontamination processes. The application is designed to ensure salt batches meet specific criteria for transfer to SWPF. That’s important to us and to our DOE customer, who has identified in the Annual Priorities and Strategic Vision that the start-up of SWPF is a top priority.
- Increasing the transfer rate of decontaminated salt solution to the SPF for permanent disposal in SDUs; both SPF and SDUs are two key components in the SRS liquid waste treatment system.
- Integrating CoreSIM, a computer modeling technology used by SRR’s engineers, which allows parameters to be adjusted to align the entire salt batch flowsheet to provide the salt waste needed to be processed each year.
In addition, the team has streamlined sampling requirements, reduced the sample analysis time, eliminated bottlenecks, and provided new improvements throughout the organization.
Constantly challenging our processes is one way we continuously improve. This concept is significant at SRR when we are implementing new technologies into how we treat and dispose of the waste stored in the Tank Farms. It shouldn’t surprise you that Continuous Improvement is one of the core values at SRR.
It’s at the heart of what we do.