Leading Indicators that Drive Cultural Improvement & Sustainability
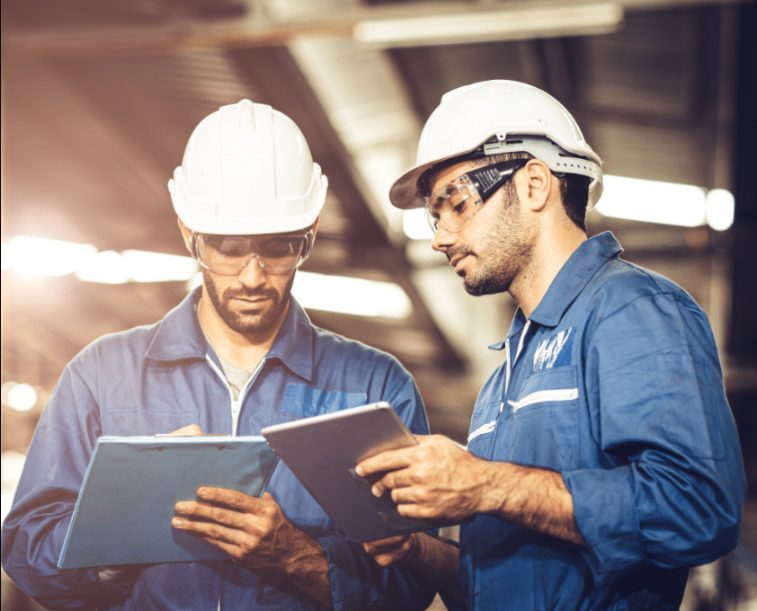
Leading Indicators that Drive Cultural Improvement & Sustainability
If your company is solely measuring safety performance by injury rates, OSHA citations, worker’s compensation cost, you are evaluating based on events that have already occurred. These types of measurements are lagging indicators. Certainly, all incidents need to be fully investigated with root cause determination so we can learn from our incidents to prevent reoccurrence. Lagging indicators cannot be ignored and are a critical component to your safety management system. But evaluating these alone is a reactive approach to safety because corrective action cannot be initiated until after the “bad” results have occurred.
On the other hand, leading indicators are proactive, preventative, and predictive measures that monitor and provide current information about the performance related to specific activities, and processes of an EHS management system. They drive the identification and elimination or control of risks in the workplace that can cause incidents and injuries. Effective characteristics of a leading indicator include:.
- Objective and easy to measure
- Relevant to your business
- Provides immediate and reliable indications of the level of performance
- Understood and “owned” by the group whose performance is being monitored
Taking these considerations into account, one size does not fit all. Leading indicators must be selected based on what works best for your organization. To get started, determine your top priorities, pick a starting point and build from there. The ultimate goal is to equip senior management with the most accurate and up-to-date knowledge in order to increase their awareness, support, and commitment to the leading indicator program. It should promote continuous improvement and must be tied to performance goals at all levels of the organization with accountability in place. Below is an example of a Leading Indicator Dashboard with six performance criteria.
Leading Indicator Descriptions:
- Training: Training requirements are identified down to the job level for all employees with completion tracking, knowledge verification and recertification requirements.
Audit: A robust auditing process that is aligned with business practices that takes a deep dive into policies, programs and the culture with corrective actions identified and tracked to closure. - Roadmap: Program requirements sites need to accomplish on a monthly basis to stay compliant.
- Employee Field Reviews and Inspections: Managers or supervisors out in the field performing targeted workplace inspections and employee field reviews while employees are engaged in work activities.
- Safety Walks: Cross-functional workplace inspections targeting different areas of the facility identifying safety issues that are tracked to closure.
- Observation program: Employee engagement with identifying and reporting safety hazards, stop work interventions, near misses, etc.
By focusing on these six leading indicators, we have seen significant improvements in our incident rates and are significantly below the average for most industries.
Realistic goals should be carefully set for each performance category. Setting goals too low will give your company a false sense of security and lead to complacency. Also, goals should be set in a way that drives improvement. For example, if you have an observation program that requires supervision to conduct a certain number of observations per month, are you only measuring if they did the required number of observations or are you also measuring the quality of those observations? If the goal becomes a check-the-box exercise that doesn’t provide any value to your program, it’s no more than a pretty color on the dashboard. A quality component needs to be built into your measurements to make sure your program is delivering the results you expect.
Communication is critical — all employees need to be aware of your leading indicator program with feedback conveyed regularly so everyone knows where they stand. When one of the metrics starts to fall below an acceptable level, it should trigger action.
Finally, recognition programs are a main component to a successful program, both for individuals and at the site level. Employees should be recognized for their participation and performance to the established goals. Examples include individual recognition for highly engaged employees in the hazard identification program, Top Sites of the Year for overall leading indicator performance, Top Area, etc.
A robust leading indicator program is an absolute necessity if you want to drive cultural change, sustainability and focus the attention and work on the identification and elimination of risks in the workplace. It is not enough to measure incidents after they occur; to get ahead of the curve, leading indicators can help create a paradigm shift and result in a proactive, predictive safety culture.